A Methodology to Develop Multi-Physics Dynamic Fuel Cell System Models Validated with Vehicle Realistic Drive Cycle Data
Applied Energy(2024)SCI 1区
Univ Politecn Valencia
Abstract
Fuel cell (FC) technology has been identified as a technically attractive solution to decarbonize the transportation sector, especially for heavy-duty vehicles. In this context, the industry and the scientific community are in need of advanced fuel cell systems (FCS) models that are able to replicate real-world operating conditions. Due to the scarcity of said models in the open literature, this study aimed to develop a comprehensive methodology to calibrate and validate multi-physics dynamic FCS models. Therefore, the key contribution of this paper is the detailed description of the calibration process for each component and the calibration order. The specific focus here was to accurately describe the behavior of the FC stack as well as the cathode, anode, and cooling circuits of the balance of plant. The model was calibrated with the aid of experimental data from a Toyota Mirai FC electric vehicle, which was predominantly retrieved from the vehicle’s Controller Area Network (CAN) bus system thereby negating the need for major intrusion into the powertrain system. The validation process was deemed successful with the model being able to truthfully replicate the characteristics of the FC vehicle operated on the World-wide harmonized Light duty Test Cycle (WLTC) 3b and US06 driving cycle. The time-resolved physical parameters such as the cathode pressure, mass flow, or the FC stack temperature were captured with high fidelity, while the overall performance parameters such as the H2 consumption in the stack and the system, and the compressor energy consumption were predicted accurately with a deviation lower than 0.47%, 1.75% and 1.89% with respect to the experimental data, respectively.
MoreTranslated text
Key words
Hydrogen,Proton Exchange Membrane Fuel Cell,Simulation,Dynamic model,Fuel cell electric vehicle,Driving cycle
求助PDF
上传PDF
View via Publisher
AI Read Science
AI Summary
AI Summary is the key point extracted automatically understanding the full text of the paper, including the background, methods, results, conclusions, icons and other key content, so that you can get the outline of the paper at a glance.
Example
Background
Key content
Introduction
Methods
Results
Related work
Fund
Key content
- Pretraining has recently greatly promoted the development of natural language processing (NLP)
- We show that M6 outperforms the baselines in multimodal downstream tasks, and the large M6 with 10 parameters can reach a better performance
- We propose a method called M6 that is able to process information of multiple modalities and perform both single-modal and cross-modal understanding and generation
- The model is scaled to large model with 10 billion parameters with sophisticated deployment, and the 10 -parameter M6-large is the largest pretrained model in Chinese
- Experimental results show that our proposed M6 outperforms the baseline in a number of downstream tasks concerning both single modality and multiple modalities We will continue the pretraining of extremely large models by increasing data to explore the limit of its performance
Upload PDF to Generate Summary
Must-Reading Tree
Example
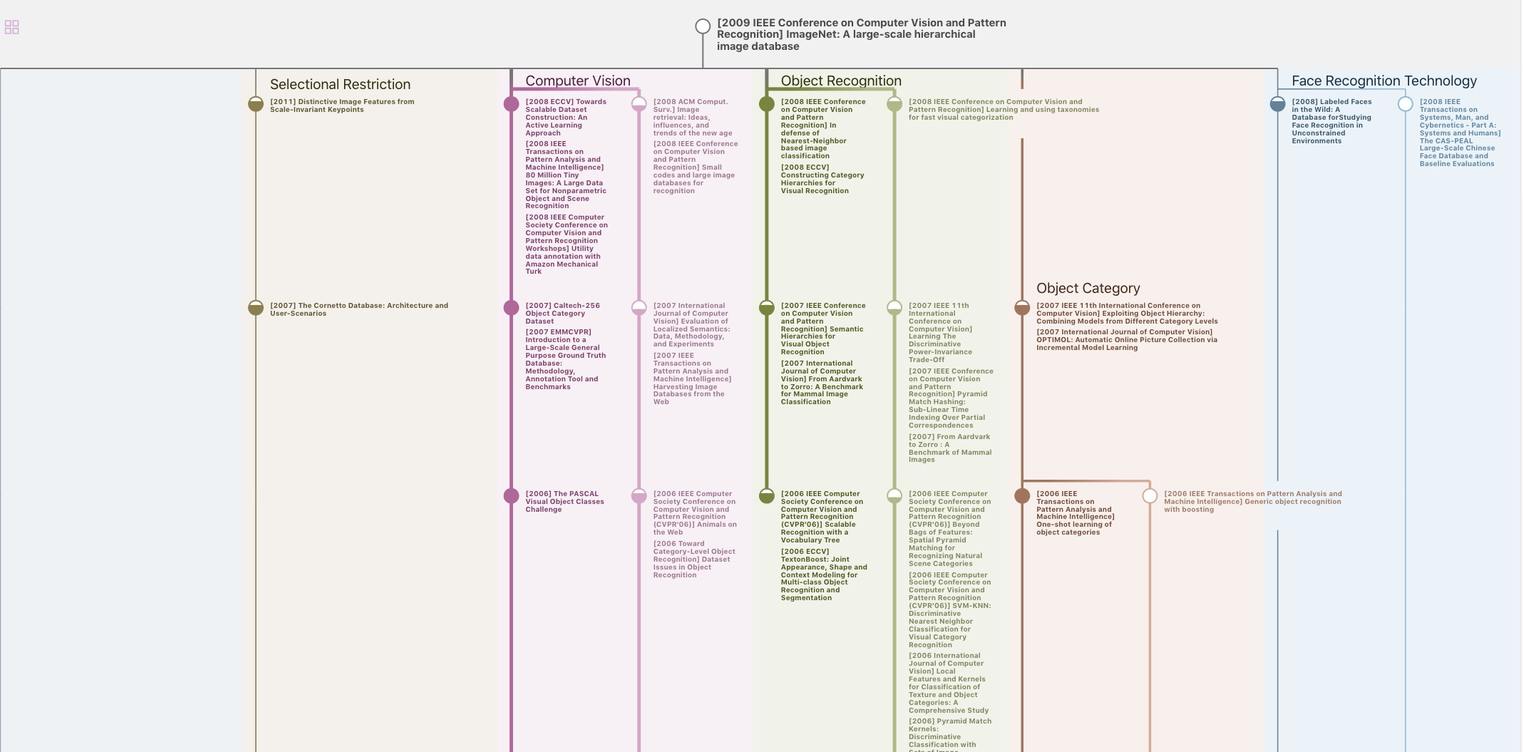
Generate MRT to find the research sequence of this paper
Related Papers
Experimental Assessment of a Heavy-Duty Fuel Cell System in Relevant Operating Conditions
APPLIED ENERGY 2024
被引用1
ENERGY CONVERSION AND MANAGEMENT 2025
被引用0
INTERNATIONAL JOURNAL OF HYDROGEN ENERGY 2025
被引用1
Data Disclaimer
The page data are from open Internet sources, cooperative publishers and automatic analysis results through AI technology. We do not make any commitments and guarantees for the validity, accuracy, correctness, reliability, completeness and timeliness of the page data. If you have any questions, please contact us by email: report@aminer.cn
Chat Paper